Podcast: Play in new window | Download (Duration: 30:00 — 41.3MB)
Subscribe: RSS
This is the WFHB Local News for Tuesday, January 4th, 2021.
This week, we will take a look back at the stories we covered in the year 2021.
In today’s episode, you will hear WFHB Correspondent Aaron Comforty report on a company that focuses on using artificial intelligence and drone technology to construct environmentally sound buildings out of natural materials.
More in Local News: 2021 In Review.
Terran Robotics: AI Meets Natural Building
The startup aims to use AI to make natural building affordable and fast.
By Aaron B. Comforty
This interview has been lightly edited for brevity and clarity.
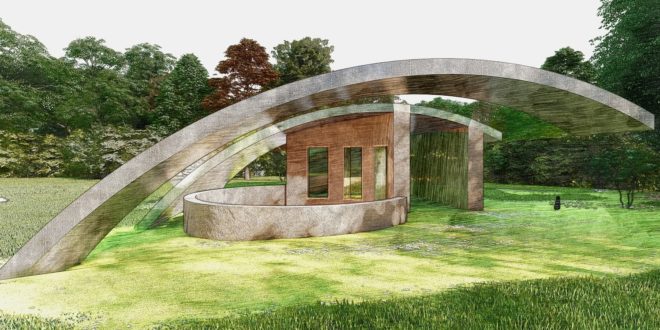
Aaron Comforty: We’ve invited the founders of the Bloomington based Terran Robotics startup onto the program. The company focuses on using artificial intelligence and drone technology to construct environmentally sound buildings out of natural materials. Terran Robotics is a recent recipient of a National Science Foundation grant worth about a quarter of a million dollars. Daniel Weddle, Zach Dwiel, and Nate O’Donnell, thanks for joining us on WFHB News. Daniel, you’ve been building tiny homes out of natural materials, for about ten years now, here in Bloomington. And as you know, this City is facing an acute housing shortage, and in the U.S. as a whole, it’s much the same story. Some analysts are predicting that the next decade will see a construction boom to meet demand. So why not use standard building methods and materials, like wooden frame construction, drywall, fiberglass insulation, and the like?
Daniel Weddle: So all of those material expenses–you could make arguments about their sustainability. Looking at automation, and the way we’re approaching building these homes, we need the simplest thing to put together, and that’s cob. It’s fairly predictable, it’s in aggregate form, and we can stack it and form it.
Comforty: What is Cob?
Weddle: It’s a mixture of clay, sand, and straw. Sometimes you’ll have portland or lime in there for stabilization, but we’re trying to stay true to form and stay with just sand, clay, and straw. Then you’ll have some kind of exterior coating on it. It can be oil, often you’ll just see more earth. Sometimes you’ll have a mixture of lime on the outside to get a little bit more weather protection.
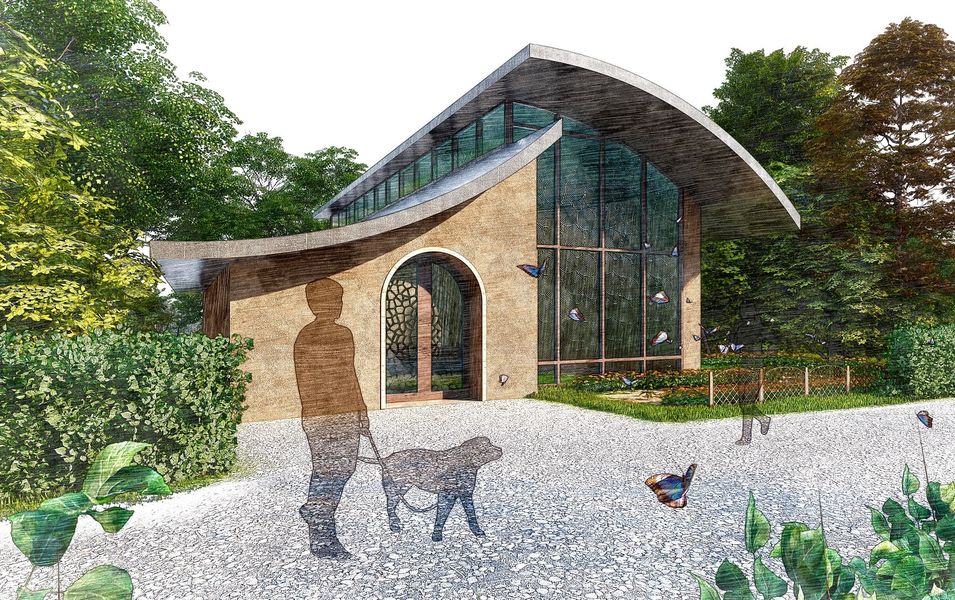
Comforty: Some of the renderings Terran Robotics has posted online are really beautiful. It strikes me as a sort of old meets new. Zach, you and Danny have collaborated in the past on natural building projects. What makes this project different? And what kind of building technologies is Terran using and developing at the moment?
Zach Dwiel: Yeah, what makes it different is just our extreme focus on what is automatable, what is cheap, and what we can do with low-cost materials. How can we use things like clay, soil, and sand to build a structure autonomously. To do the actual construction, we’re using a heavy lift drone, which can lift somewhere between 50-100 pounds, picking up cob, putting it on the wall, and also using that drone to form the wall and shape it like you would a sculpture. Eventually it would do other tasks, like picking up pavers and bricks, fiberglass mesh, ceiling panels, and all sorts of things. The benefit of the drone is that we can move anywhere on the construction site without worrying about running into stuff on the ground, having mud in inconvenient places, or having to reach really high up. It’s a very flexible platform. We can automate the walls at first but also move onto all kinds of other things, and hopefully move onto a point where we’re automating the majority of the construction process.
Comforty: Is this functional as of now? Is there any kind of precedent for using automation and drones in building more generally?
Dwiel: Sure, there are a few people at research labs, primarily, who have done proof of concept. There is a group out of ETH Zurich that has shown that kind of proof of concept in-doors. They’ve used foam blocks instead of real construction materials to build a kind of tower inside. There are things that are much more difficult in a real application. They had lots of sensors placed inside so that they could tell where the drones were flying. Those kinds of sensors you can’t run outside. There were all kinds of other things that made the project easier in a research setting as well. But generally speaking, a lot of the technology we’re using is stuff that has been developed in research labs over the past five years or so. That’s kind of my background, coming from Intel AI Research Labs. We’re just taking that research and putting it into practice.
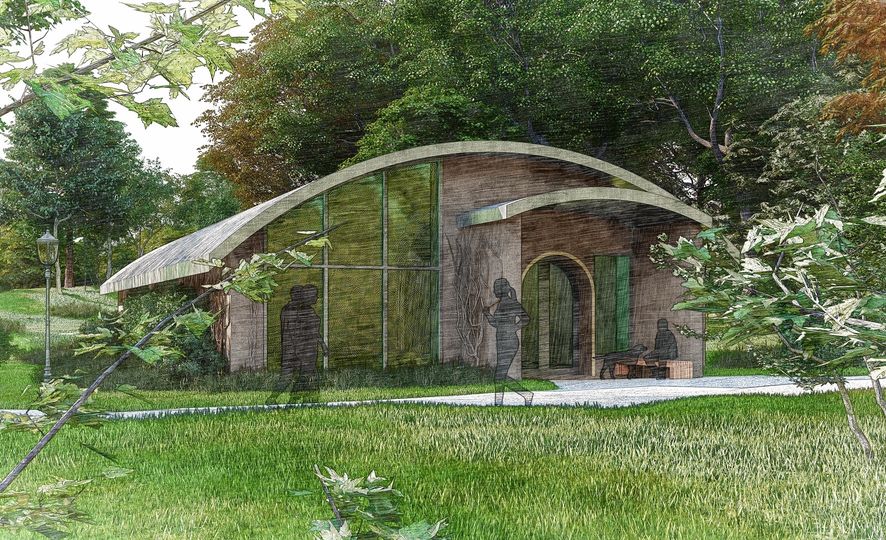
Comforty: Is there a history of using artificial intelligence, other than with drones, in construction?
Dwiel: It’s a good question. I think that maybe the closest thing would be some very beginning basic work on more generative design. It would be doing things like designing bridges which are specifically optimized in particular ways. As far as I’m aware, nobody is really using AI to actually perform construction work quite yet. There are some people who are using 3D printers to do similar kinds of autonomous construction, but those tend to not have any AI. They’re very similar to what you might expect on a smaller 3D printer or on a factory line. There’s not much intelligence in the actual machine.
Comforty: Nate, I wanted to turn to you and ask about the issues and experiences which inspired you to get involved with Terran Robotics?
Nate O’Donnell: Sure, I have known both Danny and Zach for about a decade and a half. We’ve been discussing these issues as friends for a long time, and then we kind of went our separate paths. Danny became a specialty custom home-builder, building tiny homes for the past ten years or so. Zach went in the direction of working in the field of machine learning and artificial intelligence, most recently at Intel. My background is more entrepreneurial and in marketing. I’m intensely interested in the problem that we’re trying to solve, and the big changes we’re trying to make in the world. In response to your question about why we’re using these earthen materials instead of traditional building materials, the fundamental answer is that if you look at the big picture–earthen building materials, which currently house about 30% of people on the planet, albeit, not in the so-called “developed” world, but these materials are the most abundant building materials available to us. Basically, we’re starting from first principle, and asking, ‘how can we make a house that is ten times cheaper than what’s on the market right now?’ And frankly, the materials we’re using right now are too expensive, and you just can’t do it. As a result, more and more people are unable to afford a home in the U.S.. To circle back, that’s where my interest lies with this company and the mission of the company. ‘What’s the human story? and How can we solve this intimately human problem of needing places to live?’ Obviously the money and the market come into that in a big way. I think that if we can come into the market and say, ‘We’re building these homes and they’re going to cost half the price per square foot of what’s on the market right now,” we’re going to have a big impact.
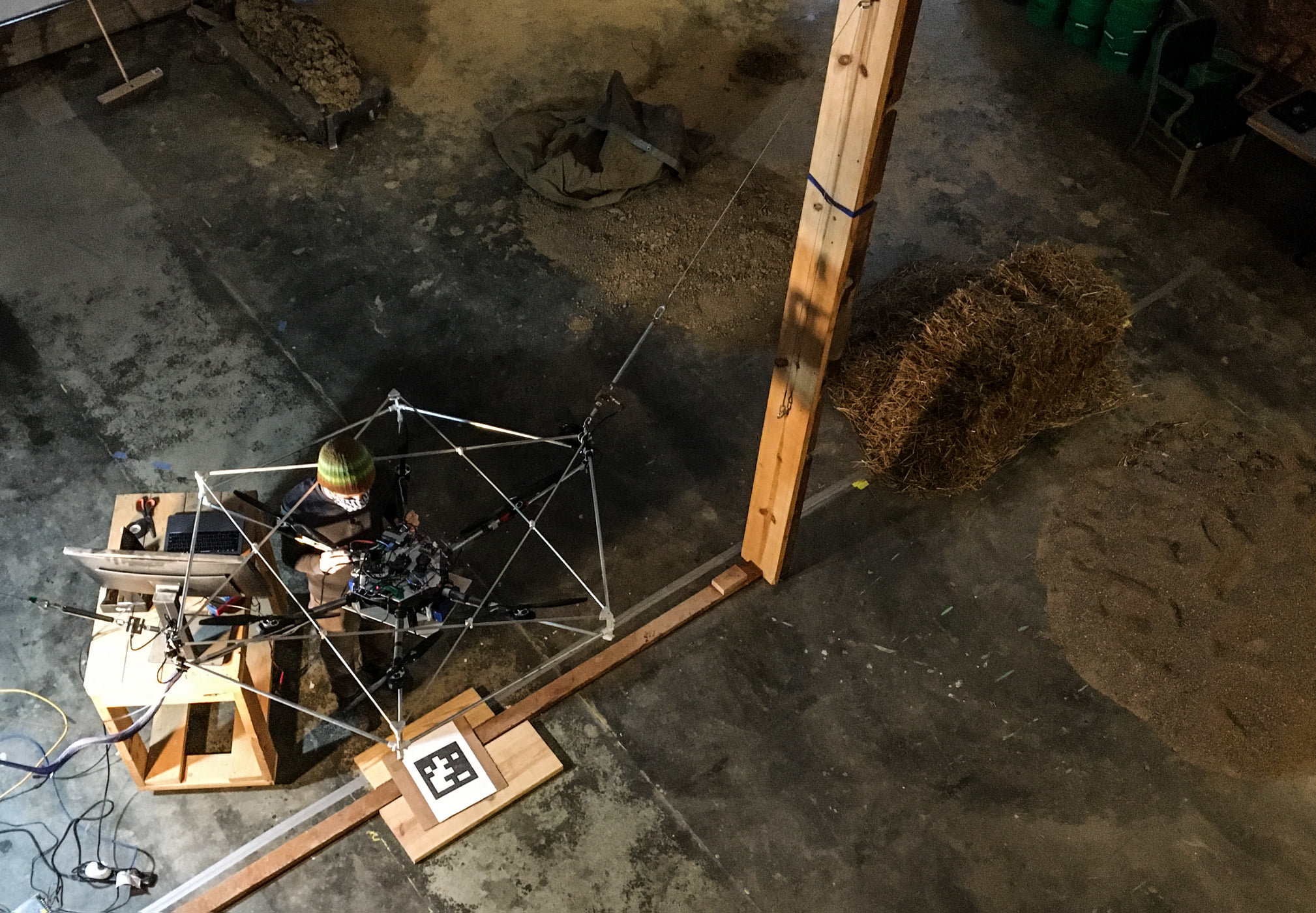
Comforty: Full disclosure, I lived in the first home that you built Danny, and the incredibly affordable rent allowed me to finish college without having to work full time. I was so lucky to live there, and I enjoyed it so much. Really, what that comes down to is housing affordability. How does housing affordability play into Terran’s future and plans?
O’Donnell: It’s a huge part of the vision and mission for the company. To put numbers to it, concrete is a relatively affordable building material. If you look at affordable housing around the world, you’ll see that a lot of it is built out of concrete. Concrete costs about $50-75 per ton. There is a little bit more complexity to it because concrete blocks have holes in them, so some of the structure is actually empty space. So suffice it to say that even if it’s half empty space or even two-thirds empty space, you’re still using a material that costs $50-75 per ton. If you compare that to earthen building materials, especially clay, in a lot of parts of the world you can use the clay that’s in the ground, and then use about three parts of clay, one part of sand, and then a pretty marginal amount of straw to produce this earthen building material, that is variously called cob or adobe, depending on where you are in the world. That mixture, you can produce for roughly $10-15 per ton, depending on your delivery costs: whether your digging it out of the ground on the building site, or whether you’re shipping it to the site. Ultimately, we’re talking about a building material that is at least five times less expensive pound per pound than the typical building material in the developed world, which is concrete. So really, the savings come from the fact that we’re building the walls, and then, soon after, the floors, which are the bulk of the structure, out of earthen material. When it comes to the rest of the building systems of the house, like the roof and kitchen–the interior finishings; we’re looking at cost savings there as well, although not as radical as the earthen material. To answer your question, that’s where the affordability is coming from. There is just inherent abundance really, and the associated low cost of those earthen materials.
Comforty: Some people might ask, ‘Why keep the price down?’ If the rest of the market is going to be at its current rate, and you can produce houses for a lot cheaper, why take the price down and make your potential profits smaller?
Dwiel: The whole reason why we started this company was to lower the cost of living significantly. The goal wasn’t just to build sustainable houses. We really wanted to pass on those savings and really wanted to provide an opportunity, like that one that you had, Aaron, where you were able to put yourself through college and have reduced rent and pursue the things you wanted to pursue because of that lower housing cost. And we really just want to see more people have that experience.
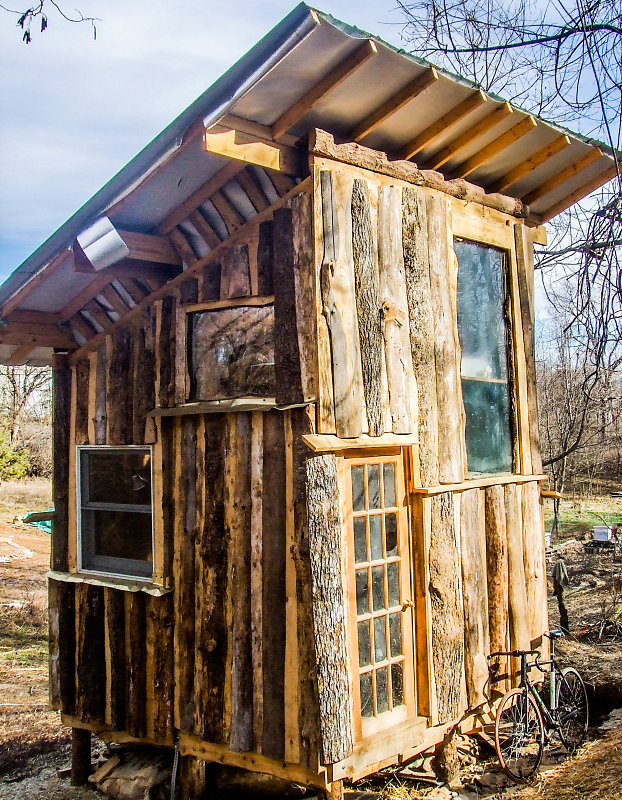
Comforty: We hear again and again about tech companies promising that their products are going democratize and improve access. And sometimes that pans out, and sometimes it doesn’t. How are you going to ensure that this project succeeds in that way?
Dwiel: By focusing on reducing the cost of living we’re cutting at inequality directly. We could build custom homes for the wealthiest people. This is often a question we get: ‘There’s a lot of people who want really fancy eco homes for millions of dollars, why don’t you sell to those people?’ Frankly, we’re just not that interested in those kinds of markets. It’s not exciting to us. We’d much rather build a future that we want to live in, with people that we want to live with. Focusing on reducing the cost of living, that’s a big part of it, but also a big part of it is the thing you were just saying for yourself, Aaron; having low cost of living means that you can spend your time doing other things, pursuing what ever it is else that you want to be pursuing.
Comforty: I want to ask you about the environmental side of this project. A lot of the standard building materials have a polluting effect. The construction industry is notable for that. We’re often talking about petroleum based products that require a significant amount of green house gases to produce. Even after they are produced, and they are in the building structure, they could still continue to pollute. We’ve seen that with some notorious examples like lead and asbestos. How do you see the environmental side of Terran relating to affordability and quality of life.
Dwiel: I think the the standard construction process is definitely very carbon intensive and very polluting. Even once a building is built there’s a lot of energy that goes into heating and cooling it. That is a significant contributor to greenhouse gas emissions. We are trying to address both of those things: how much energy the building is using as it’s being occupied, as well as the energy and pollution involved in actually creating the building. We’re definitely focused on the environmental aspects. We feel that the sustainability of the type of construction that we do is critical. We just cant can continue building in ways that are polluting and are increasing carbon emissions. There’s just no other choice. It’s almost just a given to us, as opposed to a hope or something that we want to do a little bit of. It’s more foundational–it has to be part of how we do things from now on.
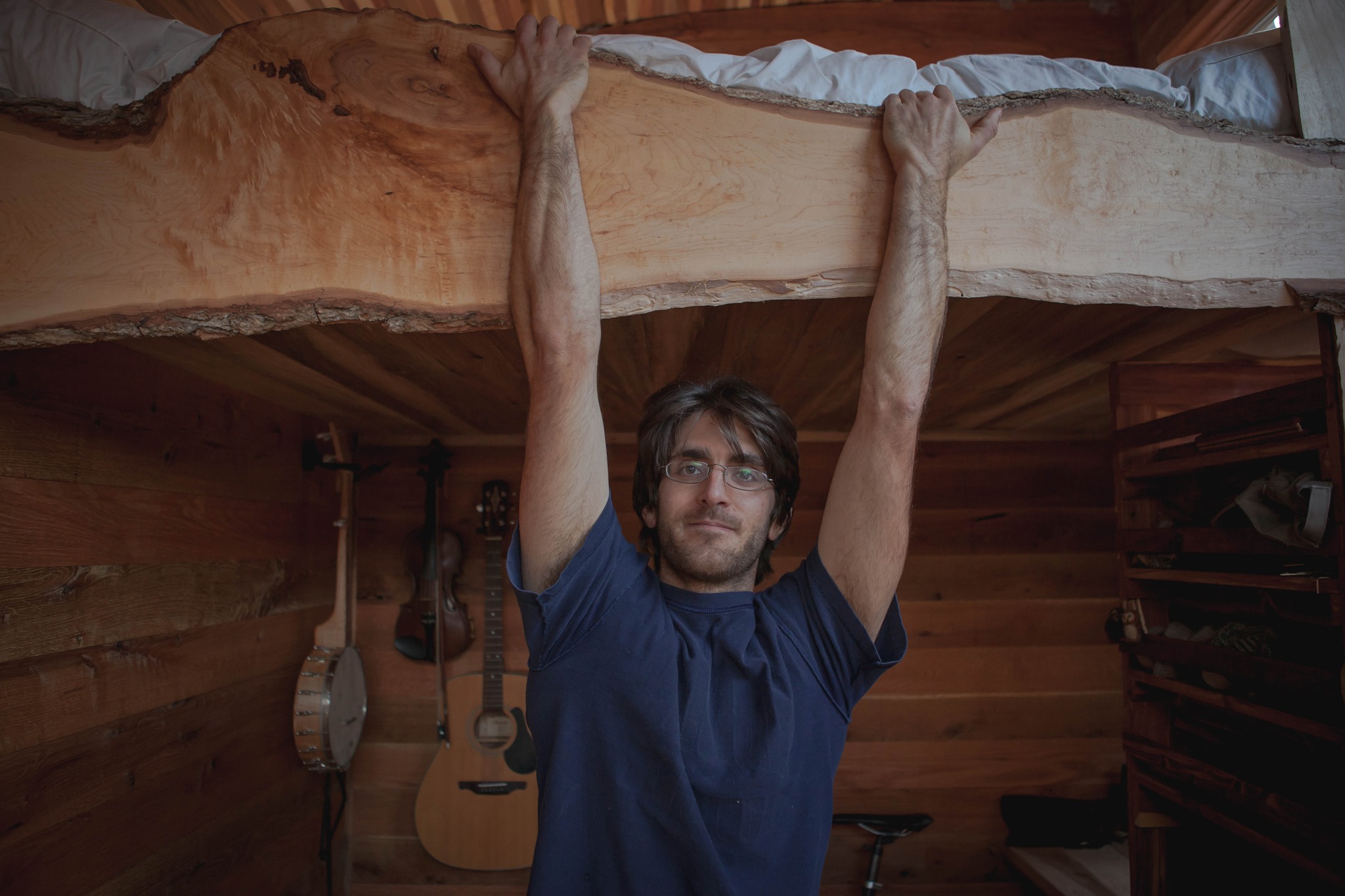
Comforty: What are some projects that Terran is dreaming up right now?
O’Donnell: This is something that we talk about quite a bit. In the short term we set our sights on designing and building a single family home that is extremely cost competitive with existing homes, and has all of the benefits that we’ve covered already. We expect to make a big impact with that. In the longer term however, to really realize the full potential of the cost savings and the benefits– we’re dreaming of community building, and providing a vision of the future that is inspiring. We kind of return to a vision that could be described as a large scale development, involving a lot of multi-family structures and community amenities. What really excites the three of us is the prospect that when you build larger developments–let’s say we were to acquire a 100 acre plot of land in southern Indiana. We could use the clay onsite to build the structures. That would save a huge amount of cost in terms of transporting the materials. From there, if you start building multi-family structures, the majority of what we’re building becomes these earthen walls and floors, because you don’t even have to insulate the interior of these buildings, and you can do things like share laundry facilities and other amenities. So the per-unit cost starts to go down. When you’re starting to talk about a housing expense of a hundred and fifty dollars per month, people can change their lifestyles to live in a more community focused way. Perhaps it will enable people to retire early, work fewer hours at jobs they don’t like, start a business, or pursue an artistic endeavor. That’s where we start to get really excited.
Dwiel: I want to echo the point that at a larger scale the savings increase significantly. Even if you make the houses for free, there’s still huge amount of cost in water treatment, the water lines, the power lines, the roads, and everything else around the house. So, longer term, we’d like be to thinking about how to reduce the cost of that infrastructure, in addition to the house, because those end up becoming a significant portion of the cost of living as the cost of the house decreases.
Comforty: It strikes me that there’s a sense of community inherent in your architecture and design. It’s been a pleasure to talk with you all. Daniel Weddle, Zach Dwiel, and Nate O’Donnell, thanks for ining us on WFHB News.
Weddle: Thanks for having us.
To see renderings of the company’s designs, sign up for Terran Robotics’ mailing list at terranrobotics.ai.
Credits:
You’ve been listening to the WFHB Local News,
Today’s feature was produced by Aaron Comforty.
Our theme music is provided by Mark Bingham and the Social Climbers.
Engineer and Executive producer is Kade Young.